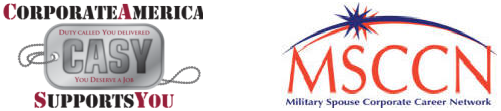
Job Information
Caterpillar, Inc. Manufacturing Engineer in Wujiang, United States
Career Area:
Manufacturing
Job Description:
Your Work Shapes the World at Caterpillar Inc.
When you join Caterpillar, you're joining a global team who cares not just about the work we do – but also about each other. We are the makers, problem solvers, and future world builders who are creating stronger, more sustainable communities. We don't just talk about progress and innovation here – we make it happen, with our customers, where we work and live. Together, we are building a better world, so we can all enjoy living in it.
JOB PURPOSE: To provide the technical expertise necessary to design, develop, and implement manufacturing systems, complex manufacturing operations and sophisticated machines.
JOB DUTIES: This is a staff position which is expected to function as a specialist with respect to a specific technical phase of the planning function and which generally falls within the major areas of planning, tooling, maintenance, plant engineering, releasing, machine shop, assembly, etc. wherever a specific technical assignment may be needed.
Work assignments may be specialized in nature but may also be broad based with coordination between other staff personnel to complete a larger project.
Develops, analyzes and manages Manufacturing Projects. Assists in developing department capital and expense budgets. Maintains the department capital forecast.
Trains new processors and develops training programs for machining operators .
Engages in creative problem solving to address operational issues including: ergonomic/ safety, efficiency improvements, process bottlenecks, quality concerns.
Works with internal and external suppliers to develop and manage projects to ensure efficient and cost effective systems and processes to produce quality products.
Provides the application, procurement, processing, installation and capability of new machining processes and equipment.
Coordinates, plans, monitors and reports the activities associated with the flow analysis, design, financial modeling and implementation of complex manufacturing group technology cells in an assigned area.
Provides manufacturing technical support in process control and internal certification.
Coordinates the corporate manufacturing and office space utilization and assists in preparation of business proposals for rearrangements or additions or complete new facilities that are being proposed to ensure proper utilization of space.
Coordinates the purchase and application of machine tools, controls and related equipment corporate wide to ensure the latest technology is being used to increase efficiency and economy of operations.
Designs complex or intricate jigs and fixtures.
Adheres to established standards, policies and practices relating to quality, cost reduction, safety, ergonomics, etc. in performing assigned duties.
Skill Descriptors
Manufacturing Equipment: Knowledge of the electrical, mechanical and logistics equipment used in manufacturing; ability to safely operate, maintain, update and store them.
Level Working Knowledge:
• Performs routine maintenance: cleaning, replacing defective or worn parts.
• Performs basic care and safety considerations for a specific type of manufacturing equipment.
• Participates in setting up new machines and testing according to manufacturer's specifications.
• Uses standard diagnostic tools and techniques; resolves common problems.
• Conducts routine inspections; checks machine performance and equipment safeguards; reports standards violations.
Manufacturing Processes: Knowledge of existing product manufacturing methods, technologies and processes; ability to execute, plan, manage and monitor the entire manufacturing process.
Level Extensive Experience:
• Advises others using industry experience and benchmarks for methodology effectiveness.
• Develops best practices documentation for all major activities and tasks.
• Trains others on all major tasks and considerations for the full manufacturing process.
• Participates in measuring and monitoring new processes and technologies.
• Selects and optimizes specific methodologies for specific products.
• Evaluates benefits, drawbacks and appropriateness of alternative processes and technologies.
Manufacturing Safety: Knowledge of manufacturing safety; ability to identify work-related hazards and perform necessary activities to meet regulatory requirements for the safety and protection of workers, environment and site.
Level Extensive Experience:
• Consults on the use of new tools and techniques for safety protection.
• Performs safety inspections to assure compliance with OSHA requirements.
• Designs and implements emergency response processes and procedures.
• Promotes workplace safety among supervisors and workers; communicates safety rules and regulations.
• Assesses and reports unusual or new safety hazards or violations; initiates corrective action.
• Ensures that all employees and contractors comply with relevant safety policies and regulations.
Manufacturing Standards, Procedures and Policies: Knowledge of organizational standards, procedures and policies in manufacturing activities; ability to plan, guide, and monitor manufacturing processes for compliance.
Level Extensive Experience:
• Consults on development and implementation of cross-functional standards.
• Participates in the development of organizational policies and practices.
• Develops and uses control and monitoring mechanisms for adherence.
• Collaborates with other functions on establishing and documenting joint standards.
• Participates in defining architectural principles and standards for organization.
• Ensures communication vehicles are effectively informing affected areas and employees.
Problem Management Process - MFG: Knowledge of manufacturing problem management processes, methodologies and techniques; ability to use a disciplined approach to bringing that problem to a successful resolution.
Level Extensive Experience:
• Evaluates alternative approaches to resolving a customer problem.
• Receives, clarifies, and resolves a variety of standard and atypical problems.
• Implements the processes and activities for handling unusual problems.
• Advises others on the process and associated costs for different types of problems.
• Monitors and improves problem reporting, tracking, escalation, and resolution.
• Participates in trend and root cause analysis to identify and address recurring problems.
Ever engaged in the introduction of 2 or more new machining centers(Vertical mills、Horizonal mills、Floor boring、Double-ended Boring Machine etc.), or at least 3 for machining centers layout adjusting.
Gained CET4 or above certification.
Preferred Skills:
Being familiar with machining 4 structures in excavator
Ever engaged in the project of automated loading /unloading for the machining center
Ever led the introduction of automatic clamping fixtures for multi-models
About Caterpillar
Caterpillar Inc. is the world’s leading manufacturer of construction and mining equipment, off-highway diesel and natural gas engines, industrial gas turbines and diesel-electric locomotives. For nearly 100 years, we’ve been helping customers build a better, more sustainable world and are committed and contributing to a reduced-carbon future. Our innovative products and services, backed by our global dealer network, provide exceptional value that helps customers succeed.
Posting Dates:
五月 7, 2024 - 五月 21, 2024
Caterpillar is an Equal Opportunity Employer (EEO).
Not ready to apply? Join our Talent Community (http://flows.beamery.com/caterpillarinc/talcom) .
There’s more to work at Caterpillar than just the work itself. We hire smart, friendly people and it shows in our culture. We hold ourselves to high standards and make sure our values of integrity, excellence, teamwork, commitment and sustainability come to life in the way we work. We make sure our employees feel continuously challenged while also supported. We provide professional growth opportunities, including leadership programs. We celebrate the diversity of our team, while also working together as one Caterpillar.
Our culture, like everything at our company, is made possible by each employee’s contribution. Person by person, we create the environment we work in, and we are proud of the Caterpillar we’ve built.
Caterpillar, Inc.
-
- Caterpillar, Inc. Jobs