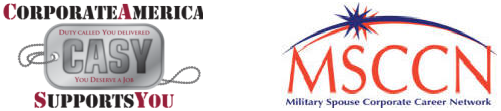
Job Information
Central States Manufacturing Plant Manager (Frame Plant) in Springdale, Arkansas
Description
Come be an Employee-Owner of one of the nation’s largest producers of metal roofing and siding! We sell, manufacture, build, and distribute metal building components and packages. Since 1988 we’ve grown to over 13 locations nationwide. We make raving fans of our customers with our “right, on time, every time” commitment.
So, who are we looking for?
People who “Own It” – Commitment to the customer, the company, and each other:You are customer-focused with an eye for detail.You are reliable.
People who “Can Do” – Our Attitude:You are an innovative thinker pursuing continuous improvement.You embrace teamwork.You want to positively make an impact and open to change.
People who “Act in Love” – Treats others with humility, respect, kindness, honesty, patience, and self-control.You enjoy giving back to your community. We take great pride in the communities we live in, so we give back with our time and talents. Each year you can take paid time off to support a cause close to your heart.
And what will you do?
Summary:
The Plant Manager is responsible for day-to-day leadership of the Pre-Engineered Metal Buildings (PEMB) rigid frame and structural steel plant in Springdale, Arkansas which is part of the Central States Building Works (BW) business providing building packages and solutions to customers across the US. The role will supervise employees, co-manage shared services in HR and logistics, develop/support initiatives to better serve customers, and maintain safety, quality, efficiency, throughput, and on-time performance. Implementing continuous improvement in process and technologies, they will exceed financial targets and work collaboratively to grow business and capabilities. We aim for best-in-industry quality, scrap, labor efficiency, delivery performance, transportation cost, key equipment utilization, net income from operations, and return on assets, while pursuing our purpose of providing for the well-being and financial freedom of our employee-owners.
Core Functions:
Creates, maintains, and supports a high performing safety-first culture. Implements and drives safety awareness behavior and applies safety, ergonomic, and environmental policies.
Personally demonstrates and builds a site culture that aligns with our purpose and values of Central States. Monitors, coaches, and mentors the team, continually improving culture and leadership at all levels within the location.
Drives proactive urgency at the site towards short and midterm goals and strategy as demonstrated by setting clear and measurable goals, which are agreed upon, communicated, and monitored constantly.
Understands the market, customers, products, and services within the Building Works business, and in the larger steel building and metal building systems industry, and translates the knowledge into strategy and plans that ensure profitable growth in line with company goals. Coaches the team and provides guidance on the execution of profitable growth strategies.
Prepares annual budgets, expertly uses financial reports and KPIs, plans annual capacity (people and equipment), and contributes to 5-year strategic plans as a member of the Building Works leadership team.
Understands and applies the “Right. On Time. Every Time.” mindset with external and internal customer relationships.
Using a Six Sigma toolkit and crucial thinking skills, the Plant Manager solves problems and prevents recurrence through detection, communication, analysis, verification, and exchange of lessons learned/best practices. Coaches others on mindset, tools, and methodologies.
Leadership Functions:
Provides leadership, support, and direction to site employees while ensuring the skills and competency of the team members are built and maintained. Coaches all team members to improve and understand basic improvement mindset, job duties, and safety.
Determines needed shifts, staffing, and performance improvements required to exceed customer expectations.
Actively collaborate with Building Works VP of Engineering and Operations to ensure plant can satisfy technical requirements of customers and that the interface and communications between engineering, drafting, and detailing and the factory is smooth and effective.
Actively collaborate with co-managed Human Resources Manager to design organization, foster culture, resolve issues, and adhere to corporate policies and standards.
Actively collaborate with shared services in IT on requirements gathering, technology specification, commissioning, and usage in the plant, integrating with accounting systems and engineering design tools and the software interfaces of the various machines and equipment in the factory
Mentors staff to optimize performance, grows and develops team through talent identification and succession planning, and drives for results and leadership growth.
Invests significant effort on talent offense and aligning training and development of teams to mindsets and skillsets important to the future of our business.
Develops and fosters effective and productive teams using ongoing performance management. Identifies and mentors high potential team members to prepare them for the next steps, including one-on-one time to have them learn from experience of doing, exposure to situation, and education for skills. Delegates as needed to team leaders to help develop them and balance supervisor workload.
Resolves conflicts between people, shifts, departments, and sites. Sets and maintains the expectation that relationships between supervisors, peers, and employees are respectful and inclusive.
Fosters a culture, including ways of working and behaviors, that is focused on a high level of teamwork, productivity, safety, and performance, while aligning with the company’s mission and values.
Promotes team building, builds trust within the team, and reacts quickly by addressing any distractions or concerns raised by employees, to have operations aligned and working towards one goal and objective. Motivates the team to always hit and exceed goals, pointing out and correcting concerns or issues.
Appraises performance of direct reports and ensures the appraisal process for Operations is effective and adheres to the company’s performance appraisal standards. Gives immediate feedback on performance concerns and frequent feedback on progress. Performs Performance Evaluations each year with all EO’s covering previous year’s performance, areas needing improvement, progress during the past year, and any personal development items that should be worked on together.
Sets area goals and objectives aligned with Site and Corporate goals/objectives. Communicates what the EO’s can do to improve the results. Creates a Line of Sight to the goals/objectives with action plans to achieve. Drives proactive urgency in team toward goals/objects that the team has agreed upon through clear communication and close monitoring.
Collaborate closely with Project Management Organization (PMO) for the build-out and commissioning of the plant and all of the related equipment, processes, and people operations.
Operations Functions:
Develops and executes a clear vision with sharply focused strategies that will ensure manufacturing operations support the overall business strategy and remain ahead of the competitive curve. Collects operational metrics to analyze productivity, efficiency, and set performance targets to meet revenue and cost goals.
Plans annual, monthly, weekly, and daily capacity (people and equipment) and budgets. Uses qualitative and quantitative approaches to determine needed shifts, staffing, and performance improvements required to exceed customer expectations. Develops and executes the plan, including capital spending needed to support the necessary performance improvements.
Works closely with sales leadership and Supply Chain departments to develop PEMB plant’s Supply & Demand and determine which action items are required to mitigate risk based on forecasted volume for upcoming months, during the monthly SIOP process.
Makes any production adjustment as soon as possible to minimize impact to the organization and eliminate impact to the customer.
Anticipates and acts on changing factors in the business environment.
Conducts problem solving activities for quality and production issues for the site. Understands a structured process to solve problems with root cause and validated corrective actions.
Monitors the site’s performance against KPI’s. Works with the team to ensure deviations (good and bad) are understood and actions are in place to address these deviations.
Understands cost control and what financially impacts the site. This includes knowing cost impact of OT, scrap, lost production time, etc.
Manages and supervises all plant operations, ensuring that the highest level of productivity, safety, and quality are always maintained.
Ensures robust plant safety inspections, auditing, and training procedures are implemented to meet OSHA and other required regulations.
Ensures understanding and compliance of all regulations, policies, and procedures relating to Safety/OSHA/Regulation controls. Constantly reinforces and stops all other activities to prioritize safety concerns.
Ensures that Quality Control, RMA corrective actions, and internal/external customer feedback are performed based on CS standards.
Ensures that action is taken on all quality issues and the results are being monitored. Fosters a Lean Manufacturing environment to continually manage and improve the plant’s quality. Trains staff to look for and report quality issues in all phases of product life.
Ensures that shift hand-offs on both sides are effective and ensures that all needed information is known between supervisors, team leads, and EO’s to allow for smooth shift starts.
Conducts production planning each day in line with CS standards and ensures that all customer requirements are met, employee well-being and production efficiency are considered. Creates, shares, and monitors production plan. Plans and balances overtime based on workload and schedules. Watches possible deviations to this plan and makes adjustments to ensure customer needs are met.
Communications Functions:
Accountable for effectively communicating with and supporting the team. This includes the timely communication of relevant information, as well as the company’s purpose, vision, and values.
Shares best practices, tools and knowledge, and works collaboratively with peers, departments, and other plants to ensure the success of the company through continuous improvement and excellence in processes and people.
Understands the standards, guidelines, and regulations applicable to the site.
Effectively communicates all safety incidents in accordance with the policy. Ensures proper analysis and treatment of incidents including “near misses.” Initiates and embraces an environment where all employees feel comfortable communicating safety concerns.
Asks clarifying questions to understand reality and determine root causes of issues.
Clarifies expectations, performance, and company initiatives.
Visually and verbally informs assigned area of performance for company, site, area, and individual.
Rewards and recognizes good performance and promptly addresses and corrects poor performance.
Posts and maintains updated work instructions at ALL workstations. Ensures that all training to the latest standard is complete and effective.
Drives Visual Factory improvements throughout the assigned area.
Communicates the overall direction of the Operations team to the site, including customer service initiatives, company and site improvement activities, and policy changes.
Duties, responsibilities, and activities are not limited to the list above and may change at any time with or without notice.
Key Measures of Success:
Deliver business results and achieves operational excellence from the factory operations including plant optimization, maintaining target cost per pound, asset utilization, labor efficiency, scrap, transportation efficiency, employee productivity efficiencies, inventory management, machine/equipment uptime, and repair cost. Must be able to handle multiple projects while maintaining accuracy, detail, and timeliness.
Understands and applies the “Right. On Time. Every Time.” mindset with external and internal customer relationships.
Able to recognize and systemically eliminate waste. Able to define and apply processes and standards. Coaches all levels of the organization on waste recognition, continuous improvement, process/standards, and lean manufacturing principles and their implementation.
Possess strong understanding of manufacturing computer systems, engineering design tools, and lean manufacturing tools.
Consistently exhibits and displays the company’s values of “Own It. Can Do. Act in Love.”
Own It – Commitment to customer, company, and each other.
Can Do – Team Player, Open to Change, & Pursuing continuous improvement.
Act in Love – Treating others with humility, respectfulness, kindness, honesty, patience, and self-control.
Education & Experience:
Bachelor’s degree in engineering, mechanical engineering, or industrial engineering, or equivalent combination of education and experience.
Minimum of 10 years in manufacturing plant leadership role, including people management responsibility with demonstrated ability to develop people, retain employees, mentor leaders, and drive high-performance teams. Preference for multi-shift environments in an organization with managers, supervisors, and leads over different functions and shifts.
Experience with plant startups preferred.
Minimum of 5 years in PEMB or metal building systems manufacturing, including familiarity with American Institute of Steel Construction (AISC) standards and experience achieving and maintaining fabrication certifications. Familiarity with Metal Building Manufacturers Association (MBMA) and the AC472 standards (through International Accreditation Service). Experience managing certified welders. Experience with automated and robotic production equipment preferred.
Minimum 3 years of experience in structural steel fabrication.
Proven experience in managing safety and environment, production efficiency, maintenance and upgrades, manufacturing systems, equipment utilization, product quality, budget, and financial cost controls.
Exceptional verbal, problem-solving, presentation, and facilitation skills, including executive communications and the documentation of technical requirements.
2+ years' utilizing lean manufacturing tools (5S, 5W2H, etc). Six Sigma training or certifications preferred.
Demonstrated experience leading and participating in safety programs, like Safety 24/7.
Physical Demands & Work Environment:
Work is performed in a combination of office and plant floor environments. This role will routinely utilize standard office equipment to perform the core functions listed in this job description. This position requires the ability to occasionally lift office products and supplies as well as communicate verbally and electronically. The work requires extensive reading to perform the core functions listed in this job description. The noise level in the work environment and job sites can be loud and in a non-temperature-controlled environment. While performing the core function of this job, the employee is regularly required to talk, hear, stand, and required to lift to 35 lbs. This position is primarily working around machinery with moving parts, working around moving objects or vehicles. The employee is frequently required to walk, use hands to finger, handle or feel, reach/pull/push/grab with hands and arms, kneel, and crouch, twist, and bend. The employee is occasionally required to sit, climb, or crawl.
Reasonable accommodation may be made to enable individuals with disabilities to perform core functions.
Travel:
This position requires up to 10% of traveling in a year.
Benefits Offered:At Central States, we are an ESOP. That means each one of our employees is an owner of the company and receives an allocation of stock every year. This allows all our employees to share in the wealth and success of the company. We also offer:
401K Match
Education assistance available – Up to $5,250 each year
Profit-Sharing bonus or own it bonus
Medical – 100% employer-paid coverage available
Dental
Vision
Holiday pay
Vacation pay
Employee Assistance Program providing Confidential Emotional Support, Work and Lifestyle Support, Legal Guidance, Financial Resources and Digital Support
Care Guides to help employees navigate the complex healthcare system
Life insurance – 1.5x annual salary – 100% employer paid
Wellness Program – earn up to $1,200 annually when enrolling in a medical plan!
Health Savings Accounts
Flexible Spending Accounts
Short-Term Disability
Long-Term Disability – 100% employer paid
Performance based merit increases
SHINE program – Employee Financial Assistance and Dependent Scholarships!
Central States Manufacturing, Inc. provides equal employment opportunities to all employees and applicants for employment and prohibits discrimination and harassment of any type without regard to race, color, religion, age, sex, national origin, disability status, genetics, protected veteran status, sexual orientation, gender identity or expression, or any other characteristic protected by federal, state, or local laws. This applies to all terms and conditions of employment, including recruiting, hiring, placement, promotion, termination, layoff, recall, transfer, leaves of absence, compensation, and training.