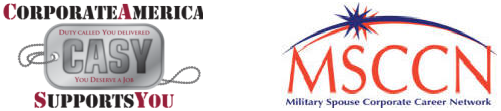
Job Information
Alamo Group Inc. Manufacturing Engineer in Seguin, Texas
Position Summary:
Under general supervision, supports the development of robotic automation welding and CNC machinery that will further increase the efficiency and the quality of the manufacture of Alamo Group products. Responsible for creating programs, jigs and fixtures and training operators. Actively participates in the development and manufacturing introduction of new products. This position will support the engineering and production process of AGTX.
Essential Functions of the Job:
Implement manufacturing techniques and processes that will reduce manufacturing labor costs, product through-put time, W.I.P. (Work In Process) inventory levels and overall manufacturing operating costs, while striving to attain World Class Manufacturing status.
Develops and implements manufacturing systems and operating procedures to support and enhance manufacturing techniques and processes.
Assists plant employees, supervisors and support personnel in the implementation and techniques of World Class Manufacturing.
Evaluates, justifies and installs new equipment and tooling to support and enhance those World Class Manufacturing techniques and processes.
Continually monitors and evaluates manufacturing labor cost indices such as efficiency, utilization and productivity to insure compliance with product cost levels.
Assists in monitoring and evaluating operating costs for compliance with budgeted operating cost levels.
Continually develops and upgrades labor standard data base for use in labor standards applications, cost evaluations and product costing.
Evaluates and recommends plant layout changes and modifications to enhance space utilization, material flow, employee safety and product throughput.
Actively participates in the development of new products to insure compliance with manufacturing and processing strategies, product quality objectives, tooling objectives, implementation dates and product cost goals.
May be required to perform other duties as assigned.
Knowledge, Skills and Abilities (KSA’s):
Knowledge of World Class Manufacturing techniques and kaizen principles.
Good communication skills, both verbal and written. Ability to communicate with various levels within the organization.
Ability to coordinate multiple activities and meet deadlines.
Ability to take direction and support all departments as needed
Experience with CAD systems, MRP systems and various communication platforms such as TEAMs.
Problem solving and troubleshooting skills required.
Basic knowledge of steel fabrication, welding, and industrial equipment assembly.
Basic knowledge of CAM systems and robotic manufacturing.
Core Competencies for Leaders:
Leading Change / Change Management: Ability to drive improvement of team, division, and corporate goals and objectives through people. Ability to balance change and continually strive to improve business performance.
Leading People / Teamwork: Ability to design and implement strategies which maximize employees’ potential and foster high ethical standards in meeting the team, division, and corporate objectives.
Communication: Ability to explain, advocate, and express facts and ideas in a convincing manner, and negotiate with individuals and groups internally and externally. The ability to develop internal and external networks and identify the issues that impact the work of the organization.
Business Acumen: Understands and interprets business financials, metrics, and utilizes latest business strategies. Focuses on outcomes and creates opportunities for success. Acquires and utilizes human, financial, material and information resources effectively.
Results Driven: Ability to make timely and effective decisions and produce results through planning and the implementation and evaluation of business metrics, systems, policies, and program; stressing accountability and continuous improvement.
Education and Experience:
Bachelor's degree in Industrial Engineering, Industrial Technology, or a related technical field is preferred.
Minimum 3 years previous background in a related manufacturing environment required.
Background and experience in a production GMAW welding environment.
Working Conditions:
Frequent sitting or standing for extended period of time. Standard office environment. Occasional to frequent walking in and around manufacturing plant or outdoors for testing.
Must be able to lift 35 pounds alone and greater than 35 pounds with assistance.
Ability to wear appropriate PPE, including hearing / eye protection, gloves and safety shoes.
Must be able to work overtime as needed to complete job assignments.
Must be able to work in and office environment and an uncontrolled outside environment.
May require occasional travel.
Alamo Group is proud to be an Equal Employment Opportunity, Affirmative Action employer. All qualified applicants will be considered without regard to race, national origin, color, religion, age, genetics, sex, sexual orientation, gender identity or expression, disability or veteran status. We maintain a drug-free workplace and perform pre-employment substance abuse testing (where permitted by law).
Alamo Group Inc.
-
- Alamo Group Inc. Jobs