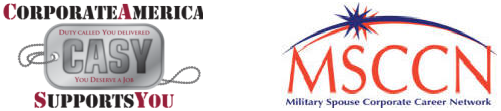
Job Information
Miller Milling Maintenance in Saginaw, Texas
Miller Milling is one of the top four flour producing companies in the United States.
Come help us make the good stuff. Because without good people to back it up, our flour is just flour. We’re always looking for dedicated people, and we offer some of the best benefits in the industry — because our team deserves nothing less. That includes full medical, dental and vision that starts on Day One, a competitive 401(k) matching program, and other perks like tuition reimbursement and flex spending accounts. To name but a few.
The Saginaw Facility is soon to be the 2nd largest wheat flour milling facility in the United States producing 34,000cwts of flour (3.4 Million Pounds of Flour) per day! Utilizing cutting-edge technology, our facility stands as one of the most advanced milling operations in the country. We pride ourselves on our commitment to quality, innovation, personal and food safety, and sustainability in every aspect of our operations.
Our team members and leaders strive for excellence, and we are constantly looking for ways to improve. We are looking for hard working individuals that can provide an immediate impact to our team. We pride ourselves on being able to work safely and efficiently to feed the great state of Texas.
Come join the team to make product to feed your family, friends, and community.
Maintenance Technician Job Responsibilities:
The Maintenance position is responsible for performing scheduled and unscheduled maintenance and repair of all equipment and plant systems.
Compensation: $28.00 - $35.00 hourly.
Primary Duties:
To perform scheduled and unscheduled maintenance and repair on all plant equipment that includes hydraulic and pneumatic equipment, as instructed and supervised by the Maintenance Manager. Including but not limited to lubrication, equipment inspection and adjustment, parts replacement, cleaning, etc.
To perform permanent or temporary repairs on all plant equipment as required ensuring continual production capacity. Such repairs may require extended and unscheduled hours without pre-notice.
To carry out needed physical improvements to all plant and equipment.
To ensure that the Maintenance Manager and current Shift Miller are immediately informed of any problem with any plant personnel or equipment which might result in an unsafe condition, inefficient operation or reduction of production.
To perform miscellaneous and unspecified duties relating to plant operation, maintenance and repair as requested by the Maintenance Manager when present or else the Shift Miller.
Other duties include prepping parts for upcoming jobs, including rollermill roll prep, belt making, spouting repairs, shop and parts organization, express maintenance data entry etc.
To carry out all duties with human safety as first priority.
Must observe and utilize Good Manufacturing Practices (GMP) as set forth by Miller Milling Company in accordance with BRC standards.
Responsibility to follow food safety regulations.
This position requires being in the on-call rotation approximately every 5 weeks, once the Maintenance Manager estimates employee is ready.
Train less experienced employees in all areas of the maintenance department.
Qualifications:
High School Diploma or equivalent required.
Strong problem-solving abilities required.
Must be able to work with the equipment and tools used to perform this job. Prior experience is a plus.
Training in Fall Protection, Forklift operation, Confined space entry, Arc flash, and other training required is preferred.
Basic computer skills required.
Detail oriented preferred.
Proven written and verbal communication skills required.
Position requires the ability to lift and carry packages up to 50 pounds.
Added Benefits in Maintenance Department:
All tools and uniforms provided by the company
Strong energetic team working together towards a common goal
World class organization and 5S programs
Laundered uniforms provided
All safety equipment provided (includes stipend for boots, prescription safety glasses, and standard PPE)
Safety lead culture