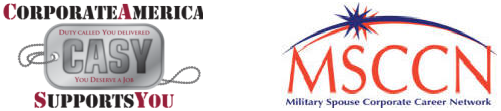
Job Information
Wabtec Corporation Site Quality Lead in Rohtak, India
Wabtec Corporation is a leading global provider of equipment, systems, digital solutions and value-added services for freight and transit rail. Drawing on nearly four centuries of collective experience across Wabtec, GE Transportation and Faiveley Transport, the company has unmatched digital expertise, technological innovation, and world-class manufacturing and services, enabling the digital-rail-and-transit ecosystems. Wabtec is focused on performance that drives progress, creating transportation solutions that move and improve the world. Wabtec has approximately 27,000 employees in facilities throughout the world. Visit the company’s new website at: http://www.WabtecCorp.com .
It’s not just about your career… or your job title…it’s about who you are and the impact you are going to make on the world. Do you want to go into uncharted waters…do things that haven’t been done to make yours and someone else's life better? Wabtec has been doing that for decades and we will continue to do so! Through our people, leadership development, services, technology and scale, Wabtec delivers better outcomes for global customers by speaking the language of industry.
Role Summary / Purpose:
Production Quality leader will lead the following in the Quality Function for Engine Reman at Wabtec’s Rohtak Plant.
Be responsible for all quality aspects of engine reman & its component. The role requires effective cross-functional stakeholder engagement for executing the above key responsibilities and meeting business goals set for the Quality Function.
Essential Responsibilities:
· Responsible for quality of all reman work including & other component as par defined OH cycle.
· Lead the Quality Inspection of reman parts & ensuring no escapes from the station and in full compliance with the MIP (Manufacturing Inspection Plan) and in compliance with the approved WPS and Wabtec standards.
· Review process requirements/CTQ’s and make sure they are met.
· Work with CFT (ME, Materials, Engineering, etc) to establish quality requirements during process setup & PPAP phase.
· Raise NCMR (Non-conforming material report) and follow up with stakeholders for its disposition.
· Train and manage ops team for quality control technicians (Team members or line Supervisor).
· Set standards for quality considering health and safety.
· Look at ways to reduce waste and increase efficiency. Able to perform RCA & CAPA.
· Able to prepare SoD (Strength of defence) for corrective actions.
· Preparing & reviewing PPAP or other Management of Change (MOC) documents (in case of manufacturing process change or introduction of new processes) and assess the effectiveness of changes made.
· Ensure quality performance, alerts, and other relevant information is communicated effectively through multiple media approaches.
· Updating existing Quality documents as per QMS.
· Set up and maintain Quality controls (MIP) and documentation (Quality Alerts, Stand downs) in Reliance and Oracle online tools.
· Monitor performance by gathering relevant data and produce statistical reports and drive projects (with partners such as operations and engineering) to meet specific quality metrics such as internal defects, scrap/losses, escaping defects, and infancy failures.
· Liaise with other stakeholders and provide training, tools and techniques to enable others to achieve quality standards.
· Prepare Internal audit schedule (Process Audit) and adhere to timelines.
· Weekly/Monthly reporting and documentation with zero quality escapes to next station
· Oversee site special process program(s) (e.g., nondestructive testing, welding), gage calibration, cleanliness (i.e., Millipore lab), external destructive testing, and training records.
· Act as main focal point for customer visits, audits, and other 3rd parties as related to quality.
· Undertake and drive special projects for reducing NCMR / quality defects from time to time.
· Design/Develop and own all documentation for plant production
Qualifications / Requirements:
Bachelor’s degree in mechanical / Electrical / Production /Industrial Engineering
Minimum 8 – 12 years of professional experience in Quality Assurance & Quality control or Process Engineering in Rolling stock Manufacturing and Testing or similar industry type (eg. automotive, power plant, Heavy Machinery). Strong background in the interpretation of Engineering drawings /Stack-up Analysis/Specifications & Manufacturing processes
Ability to Review drawings, plans, and specifications along with the manufacturing engineer and to incorporate the requirements into the Quality Plan / procedures. Sound knowledge in PPAP, APQP, Six Sigma, Structured Problem Solving, 7QC Tools. Sound knowledge of Assembly Process, Interfaces, Troubleshooting etc. Knowledge of welding process like SMAW, GMAW, FCAW and NDT Level-II, Conversant with AWS codes and ASME, Section-IX standards. Experience in defining/generating / maintaining ISO-9001 QMS documentation, undertaking process audits, Highly proficient in MS-Office and Oracle, Mini Tab
Desired Characteristics:
Self-directed, highly detail oriented, organized, & flexible
Excellent interpersonal skills with the ability to work closely with diverse team members on shopfloor and with cross functional stakeholders
Demonstrated oral/presentation & written communication skills
Six sigma green belt certified
ISO Lead auditor.
Wabtec Corporation is committed to taking on the world’s toughest challenges. In order to fulfill that commitment we rely on a culture of leadership, diversity and inclusiveness. We aim to employ the world’s brightest minds to help us create a limitless source of ideas and opportunities. We believe in hiring talented people of varied backgrounds, experiences and styles…people like you! Wabtec Corporation is committed to equal employment opportunity regardless of race, color, ancestry, religion, sex, national origin, sexual orientation, age, citizenship, marital status, disability, gender identity or expression, or protected Veteran status. If you have a disability or special need that requires accommodation, please let us know.
Wabtec Corporation
-
- Wabtec Corporation Jobs