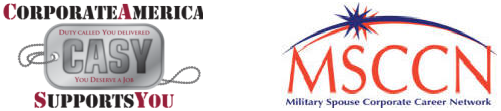
Job Information
Fortive Corporation Production Planner in Norwich, United Kingdom
Day in the Life of a Master Scheduler
A day in the life of the Master Scheduler is to review incoming customer orders against the factory production and material schedule to ensure customer-scheduled shipment dates are kept up to date.
The Master Scheduler also liases with the Production Team Leader(s) on assembly/technician resources to frequently update Distribution Centers on Shipment plans.
The role offers significant levels of flexibility in the day-to-day schedule, allowing the ideal candidate to define their own schedule, set production priorities, and optimize processes as they see fit.
Responsibilities
Responsible for the scheduling of all manufacturing priorities, including but not limited to, Build, Test, Calibration, and Shipment priority in cooperation with Production Team Leaders
Communicates the overall Production plan/capabilities to supporting functions including Finance and Customer Service to ensure seamless business forecasting and customer expectation management.
Prepares monthly PSI plan (Production, Sales & Inventory) for review and approval by the Operations Manager prior to submitting into Forecast.
Maintains the “Line of Balance” charts for Operations, to ensure visibility of the production plan for the Materials team and awareness of potential shortages.
To create, maintain, and schedule open WIP (Work In Progress) Jobs in the Fluke ERP system (Oracle) to ensure correct reflection of customer demand.
Uses the Daily Management process to monitor team performance, drive production priority, focus, and prioritize production support activities.
Advises the Operations and Production Manager on gaps in customer demand and where PDBL (Past Due Backlog) and OTD (On Time Delivery) misses will be present to escalate key production issues.
Responsible for the implementation of FBS (Fortive Business System) within the Scheduling function, such as implementing/maintaining Standard Work, following the PSI process, and a general understanding of relevant FBS Tools.
Your Team
Your core team will be centered between you and the existing Master Scheduler, however, you would all frequently interact with 3 Production Team Leaders, the Production Manager, Buyer/Planners, and the Technician Supervisor.
The team has a significant level of product and process expertise and are passionate about creating the best quality electrical, temperature and pressure calibration products in the world!
Experience
Prior experience with complex production scheduling and communication is essential, as you will be the center of factory-to-customer communication.
Previous experience may be in a role such as Production Planner, Production Team Leader, Production Manager, Manufacturing Supervisor, etc.
Personal Skills
Prioritization skills
Self-Starter
PC Literacy including Microsoft Office, preferably (but not essential) also Jira/Confluence & Oracle
Excellent communication skills
Advanced Microsoft Excel knowledge desirable (Complex Formulas, Macros, VBA)
Why you should join Fluke
In addition to the employment benefits below, this role gives the ideal candidate ample opportunity for development in lean production principles and implementation.
Being such a varied role, the candidate has a unique opportunity to put their “stamp” on the processes within the factory in order to achieve excellent levels of performance to Fluke’s customers.
Competitive Starting Salary
Private Healthcare Coverage
Private Dental Coverage
On-site events such as Summer BBQ, Christmas Lunch
Company Matched Pension at 5%
Life Insurance at 4x Annual Salary
25 Days Annual Leave + Bank Holidays
Fortive Corporation Overview
Fortive’s essential technology makes the world stronger, safer, and smarter. We accelerate transformation across a broad range of applications including environmental, health and safety compliance, industrial condition monitoring, next-generation product design, and healthcare safety solutions.
We are a global industrial technology innovator with a startup spirit. Our forward-looking companies lead the way in software-powered workflow solutions, data-driven intelligence, AI-powered automation, and other disruptive technologies. We’re a force for progress, working alongside our customers and partners to solve challenges on a global scale, from workplace safety in the most demanding conditions to groundbreaking sustainability solutions.
We are a diverse team 18,000 strong, united by a dynamic, inclusive culture and energized by limitless learning and growth. We use the proven Fortive Business System (FBS) to accelerate our positive impact.
At Fortive, we believe in you. We believe in your potential—your ability to learn, grow, and make a difference.
At Fortive, we believe in us. We believe in the power of people working together to solve problems no one could solve alone.
At Fortive, we believe in growth. We’re honest about what’s working and what isn’t, and we never stop improving and innovating.
Fortive: For you, for us, for growth.
Ready to move your career forward? Find out more at careers.fortive.com (https://stgfortive.taleo.net/enterprise/careers.fortive.com) .
Fluke Corporation is the world leader in the manufacture, distribution and service of electronic test tools and software. We are a dynamic market leader with sound financial health. Fluke has achieved the number one or number two position in every market in which it competes. The Fluke brand has a reputation for portability, ruggedness, safety, ease of use and rigid standards of quality. A wholly owned subsidiary of Fortive Corporation (www.fortive.com), Fluke is a multi-national corporation headquartered in the greater Seattle area. We offer an entrepreneurial environment that is team-centered, customer-driven, quality-focused, and growth-oriented. It is driven by the phenomenally successful Fortive Business System. Working at Fluke gives you access to a robust career development process and challenging, “stretch” opportunities
Fortive Corporation
-
- Fortive Corporation Jobs