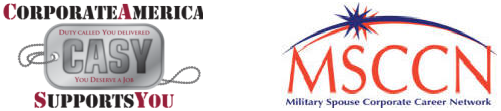
Job Information
WestRock Company Production Supervisor in North Chicago, Illinois
Job Summary: The Manufacturing Supervisor is responsible for the safe and efficient operations of production in the facility. In addition, the Manufacturing Supervisor will communicate performance expectations to shift workers, monitor production demands, supervise machine productivity and quality, and manage personnel daily.
Major Job Responsibilities:
Business Excellence
• Execute safety briefs to crews on a shift, daily, weekly, monthly and annually
• Monitor workplace safety environment to identify and address any unsafe conditions
• Ensure compliance with company safety policies, safe work practices, and plant policies
• Monitor and track production daily goals for the Corrugator or Converting machines utilizing Key Performance Indicators (KPIs) and report results on the plant scorecard
• Report all overruns, shortages, equipment breakdowns and tooling issues on the daily shift report to exchange information with all departments in the plant
• Supervise daily production activities, including oversight of team members, and monitor performance levels of each team member
• Monitor and participate in Daily Management Systems (DMS) to track progress against production goals and enable performance excellence
• Oversee production demands and machine workloads throughout the day
• Sustain productivity levels by properly staffing machines and equipment to meet customer demands and align any last-minute scheduling changes
• Troubleshoot machines issues and quality defects that may arise throughout the shift
• Ensure proper operations of equipment by requesting maintenance repairs and/or submitting maintenance work orders
• Develop, analyze and review a variety of operational reports across the functions to improve quality, efficiency, cycle times, and volumes, and implement operational changes
• Ensure quality standards are within accurate specifications for each order
• Perform audits for safety, machines and housekeeping
People and Culture
• Manage workforce planning, including fulfillment of work schedules and adherence to attendance policies (vacations, floating days, call ins, etc.)
• Communicate effectively with all functional areas of the plant to ensure all production needs are successfully achieved
• Maintain a positive relationship with the Union to align business needs and requirements
• Promote positive employee relations and interdepartmental communication and collaboration
• Provide recommendations on disciplinary action and recommend potential improvements, as necessary
Critical Skills / Capabilities:
• Communication: Creates and delivers engaging presentations to internal and external audiences; develops new communication strategies and approaches to communicate data, insights, and critical messages resulting in clear understanding • Problem-Solving: Applies knowledge to frame, simplify and solve complex issues; focuses on identifying root causes to create solutions in a timely and decisive manner; reconciles conflicting and/or incomplete information to develop solutions
• Leadership: Leads and motivates a team of people to achieve performance excellence; ability to read people and situations and adjust approach accordingly; proactively leads and enforces initiatives that drive organizational effectiveness; teaches others how to build trust-based relationships
• Coaching: Provides people with tools, knowledge, and opportunities to develop themselves; determines employees’ training needs, works with employees to produce continuous development plans, and provides regular feedback and coaching to help employees develop in current and future roles; visibly supports culture and teams • Organizational Skills: Plans, arranges and/or monitors work to ensure achievement of desired results; establishes a systematic course of action to accomplish objectives • Growth and Results Oriented: Delivers personal or organizational results by successfully influencing others (i.e. co-workers, other teams, external partners, etc.) within a matrixed organization; delivers high quality work within the stipulated time period to achieve maximum results
Technical Skills:
• Microsoft Office - Excel, Outlook, PowerPoint, Word
• Plant programs:
o AS/400
o Kiwi planner software
o Factory Floor Feedback software
• Corrugator:
o Wet End: Singlefacers, Rollstands, Splicers, Bridge, Doublebacker etc.…
o Dry End: Shear, knife, Slitter, Stackers etc.
• Converting:
o Labelers
o Rotary Die Cutter
o Flatbed Die Cutter
o Flexo Folder Gluer
o Folder Gluer
• Industry product knowledge
• Safety acumen
Other Qualifications: To perform the duties of the job, this role requires:
• Constantly reaching by extending fingers on two hands
• Constantly reaching by extending two arms
• Constantly using fingers to grasp with two hands
• Constantly using fingers to pinch with two hands
• Constantly using fingers to type with two hands
• Occasionally ascending/descending stairs
• Occasionally exerting force by pulling up to 50 lbs of weight
• Occasionally exerting force by pushing more than 50 lbs of weight
• Occasionally exerting force by lifting up to 50 lbs of weight
• The spoken exchange of ideas to be performed loudly 50-75% of the time
• The spoken exchange of ideas to be performed quickly 25-50% of the time
• Ensure the safe and accurate determination of accuracy and neatness of work or making general observations of facilities or structures
Work Environment:
• Constantly works indoors in an environment that is not climate controlled and has high temperatures
• Frequently works indoors in an environment that is not climate controlled and has low temperatures
• Occasionally works indoors, in an environment that is climate controlled
• Occasionally works outdoors in natural environmental conditions (both hot and cold)
• The role is occasionally sedentary, which entails sitting or being stationary
• Frequently stands or walks for 1-2 hours at a time
• Frequently stands or walks for 3-6 hours at a time
• Occasionally stands or walks for over 6 hours at a time
• Noisy industrial work environment; maintain strict adherence to safety rules and regulations
Experience:
• Required: 3 to 5 years of manufacturing experience or working in a production environment
• Preferred: Corrugator experience with the specifics as listed above.
• Preferred: Converting experience with various machines centers as listed above.
Education:
• Required: High school diploma or G.E.D.
• Preferred: Bachelor’s degree
WestRock (NYSE:WRK) partners with our customers to provide differentiated paper and packaging solutions that help them win in the marketplace. WestRock's team members support customers around the world from locations spanning North America, South America, Europe, Asia and Australia. Learn more at www.westrock.com.
WestRock is an Equal Opportunity Employer. We strive to create and maintain a diverse workforce where everyone feels valued, respected, and included. WestRock does not discriminate on the basis of race, color, religion, national origin, sex, age, disability, veteran status, sexual orientation, gender identity, or any other basis protected by federal, state or local law.