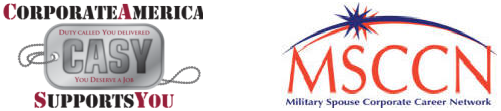
Job Information
The Moab Brewery Brewery Supervisor in MOAB, Utah
The brewery shift supervisor will be a generalist, responsible for executing a multitude of daily tasks. While the primary responsibilities relate to activities in the brewhouse, this position also will require oversight of the cellar. The position requires the training and supervision of other brewery and cellar staff members. This position requires exceptional time management and communication skills, the ability to multitask, high attention to detail and an uncompromising commitment towards quality and improvement.
Responsibilities include but are not limited to:
- Ensure execution of the plans and activities for the shift in production volumes.
- Ensures that all the work and activities are done in line with the quality standards.
- Ensure cleanliness and sanitation of environment and equipment in accordance with QA/QC standards.
- Adhere to SOP's to elevate process control and minimize variability from operator to operator.
- Training, guiding, and supervising other brewery and production staff members on all brewing and production processes
- Management of yeast health and pitching, fermentation schedules, Yeast harvesting and dumping, racking, dry hopping, and carbonation
- CIP of brewhouse, fermentation vessels and other equipment in accordance with the Master Sanitation Schedule
- General maintenance, organization, and cleaning of the brewery and cellar areas
- Fill shifts as necessitated by vacations, staffing levels, necessary overtime
- Wort production
- Draft system cleaning
- Quality checks, record keeping, and completion of check lists.
Requirements and candidate attributes
- Passion for great beer
- 3-5 years of production brewery experience
- High School degree or equivalent required
- Diploma from a technical brewing education or equaling experience
- Excellent written and verbal communication skills
- Excellent time management, leadership, organizational, interpersonal skills and to maintain positive morale in the workplace
- Basic understanding of industrial equipment including low pressure boilers, industrial refrigeration, air compressors, and pneumatic systems
- Basic understanding of plumbing, mechanical and electrical systems
- Strong computer skills with proficiency in Word, Excel
- Ability to think critically, troubleshoot, take initiative, and escalate issues to management
- Ability to work a flexible schedule, including occasional nights and weekends
- Ability to work on your feet in a loud, temperature variable environment
- Ability to work well under pressure in a fast-paced environment
- Ability to continuously lift 55 lbs. and maneuver 165 lb. kegs
- Ability to operate a forklift and pallet jack
- Abide by company PPE standards, chemical handling, and good manufacturing practices.