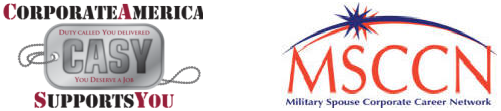
Job Information
In-Place Machining Co., Inc. Machine Shop Supervisor in Milwaukee, Wisconsin
Machine Shop Supervisor
Milwaukee, WI (http://maps.google.com/maps?q=3811+N.+Holton+St.+Milwaukee+WI+USA+53212)
Description
Summary
Responsible for scheduling and job performance for the Machine Shop (CNC & manual) taking into consideration cost, quality and production time restraints.
Essential Duties & Responsibilities
This list of duties and responsibilities is not all inclusive and may be expanded to include other duties and responsibilities as management may deem necessary from time to time.
Daily Core Tasks:
Prioritize, schedule, and delegate work assignments to ensure the following:
Jobs are completed on-time
Quality specifications are met
Costs are controlled and within budget, including but not limited to the following:
Raw Materials
Subcontracted Processes
Direct Labor
Plan machining production schedules.
Establish and define internal and outsourced machining manufacturing processes
Active participant in the selection of tools for CNC machining
Review parts shortages with Purchasing and adjust schedules as necessary
As required, establish and define components that require outsourced manufacturing processes
As required, establish process routings for component parts, sub-assemblies and assemblies
As required, establish labor standards for component parts, sub-assemblies and assemblies
As required, submit RFQs, create and issue purchase orders
As required, select raw materials when not defined.
As required, be an active participant in quoting jobs.
As required, act as a technical resource to address and resolve inquiries and problems
Project Management Tasks:
Manage all aspects of machining (jobs), including but not limited to the following:
Kick-off Meetings
Order material(s)
Manage assigned sub-contractors, specifically those defined within the SME responsibility
Routings
Labor
Post Job Review and Summary write ups
Properly communicate both internally and externally to ensure all parties are in alignment. Mark up prints to provide clear communication. Utilize tools such as email, spreadsheets, ERP reports and Gantt charts.
Subject Matter Expert Tasks:
Act as a Subject Matter Expert for assigned functions, including but not limited to the following:
Management of internal processing on assigned equipment, processes and/or skillsets
Management of external processing on assigned equipment, processes and/or skillsets
Training of personnel on assigned equipment, processes and/or skills
General Management Tasks:
Actively participate in establishing and driving 5s culture and standards
As required, perform personnel reviews, assessments, interviews and terminations
As required, participate in the evaluation and purchase of new capital equipment
As required, visit, assess and select subcontractors
Ensure the training of new and present employees in the processes and methods required to achieve the company’s standards for quality, productivity and safety
Ensure adherence to ISO 9001 procedures and requirements
Ensure the completion of all required production paperwork, records, and documentation
Ensure compliance with departmental housekeeping standards and all safety and work rules and regulations
Maintain departmental supplies, tools, equipment, and order as necessary
Approve vacation schedules
Other duties and responsibilities as assigned
Requirements
Qualifications
To perform this job successfully, an individual must be able to perform each essential duty satisfactorily. The requirements listed below are representative of the knowledge, skill, and/or ability required. Reasonable accommodations may be made to enable individuals with disabilities to perform the essential functions.
Education
High school diploma or GED
Journeyman Machinist or Tool and Die
Experience
Seven to ten years of progressively responsible related experience. Specifically, this position requires:
Extensive experience (10-15 years) with CNC Vertical Machining Centers
Extensive experience (10-15 years) with CNC Turning Centers
Proficient Experience (5-10 years) with CNC Horizontal Machining Centers
Extensive knowledge and ability with high tolerance (0.0005”) machining
Extensive experience with FANUC controls
Extensive experience with Okuma controls, preferred
Experience in low volume and high mix environment
Experience with tooling, fixturing or gaging assemblies
Extensive knowledge of GD&T and blueprint reading
Extensive knowledge of G-code programming
Extensive knowledge of machine setup principles
Extensive knowledge of feeds & speeds
Extensive knowledge of tooling for CNC equipment
Extensive ability to read and interpret blueprints & mechanical drawings
Extensive ability to program using a CAM system, preferably Mastercam
Experience in process improvement and Lean Manufacturing
Language Skills
Ability to read and interpret documents such as safety rules, production schedules, purchase orders, maintenance instructions, and procedure manuals. Ability to write reports, procedure manuals, and correspondence. Ability to communicate effectively with customers, vendors and other employees of the organization.
Mathematical Skills
Ability to add, subtract, multiply, and divide in all units of measure, using whole numbers, common fractions, and decimals. Ability to apply concepts such as fractions, percentages, ratios, and proportions to practical situations. Solid understanding of the fundamentals of plane and solid geometry and trigonometry.
Reasoning Ability
Ability to solve practical problems and deal with a variety of concrete variables in situations where only limited standardization exists. Ability to interpret a variety of specifications and information furnished in written, oral, diagram, or schedule form.
Extensive ability and desire to be a servant leader
Extensive ability to multi-task in a fast-paced environment
Extensive ability to work effectively in a collaborative team environment
Extensive ability to solve problems using critical thinking skills
Extensive ability to organize and manage priorities, meet deadlines, and expectations
Supervisory Responsibilities
Carry out supervisory responsibilities in accordance with the organization’s policies and applicable laws. Responsibilities include training employees; assigning and directing work; appraising performance; rewarding and disciplining employees; addressing complaints and resolving problems.
Physical Demands
The physical demands described here are representative of those that must be met by an employee to successfully perform the essential functions of this job. Reasonable accommodations may be made to enable individuals with disabilities to perform the essential functions.
While performing the duties of this job, the employee is frequently required to sit; use hands to finger, handle, or touch objects, tools, or controls; and talk or hear. The employee is occasionally required to stand and walk. The employee must occasionally lift and/or move physical products (up to 50 lbs), reports, files, etc. Specific vision abilities required by this job include close vision, depth perception, and the ability to adjust focus.
Work Environment
The work environment characteristics described here are representative of those an employee encounters while performing the essential functions of this job. Reasonable accommodations may be made to enable individuals with disabilities to perform the essential functions.
In-Place Machining Company is an Equal Opportunity Employer. All qualified applicants will receive consideration for employment without regard to race, color, religion, sex, sexual orientation, gender identity, national origin, or protected veteran status and will not be discriminated against on the basis of disability.