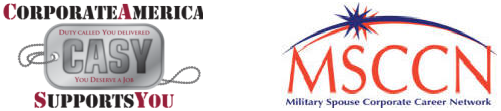
Job Information
American Battery Solutions Quality Compliance Engineer in Lake Orion, Michigan
Job Summary The Quality Compliance Engineer is responsible for ensuring the processes are defined, and compliant with the ISO 9001 and IATF 16949 standards. In the event there are non-conformances this role will quickly and effectively take necessary actions to identify root-cause analysis and partner with process owners and operations to resolve discrepancies. The Quality Compliance Engineer will lead internal audit activities to ensure successful maintenance of ISO901 certification and compliance with the IATF 16949. Responsibilities * Develops compliance plans by researching, and applying compliance engineering concepts, and criteria, developing and evaluating new compliance methodologies. * Determines compliance by establishing compliance test standards performing diagnostic procedures; measuring performance; analyzing and evaluating findings; support troubleshooting failures. Organizes compliance program by preparing timetables, cost estimates, and required resources including test laboratories and equipment. * Attains compliance by isolating and resolving non-compliance issues; recommending product and process changes; initiating engineering change orders. Prevents compliance issues by collaborating with engineering planning and design teams; reviewing design data; identifying and resolving product and engineering design issues; researching and identifying applicable regulatory and industry compliance standards and codes; developing compliance policies. * Documents compliance by completing DCS approval applications; recording test results; preparing investigative reports; maintaining compliance database. * Updates job knowledge by tracking and understanding emerging compliance engineering practices and standards. Enhances engineering and organization reputation by accepting ownership for accomplishing new and different requests; exploring opportunities to add value to job accomplishments by establishing requirements for applicable standards. * Able to gain the commitment of both internal departments and supplier organizations to remedy non-conforming practices while maintaining positive and productive working relationships. * Process checks, approvals, and audits. Review & approve manufacturing & quality data and Product Sign Offs. Develop, collect, and report leading metrics of internal and supplier performance to cross-functional management. * Coordinate pre-launch production trial run process monitoring. As well as communication with, and transfer of knowledge to, the Production Manufacturing/Quality Team. Maintain Control Plans and FMEAs throughout the life of the part. Participate in the development of Failure Mode and Effects Analysis (FMEA). * Facilitate and promote the use of appropriate problem-solving techniques for effective root cause analysis and successful corrective action. Report and track issues through JIRA. * Adhere to federal and state regulations. * Adhere to all company policies, processes, and procedures. * Performs other duties as requested, directed, or assigned. * Predictable and reliable attendance. Position Qualifications * Bachelor's degree in Engineering or technical-related field required. * Minimum of five (5) years of experience managing a certified quality management system (e.g., TS 16949, ISO). * Exceptional mechanical aptitude (i.e., intuitive understanding of mechanical processes). * Minimum of four (4) years of a proven track record of driving continuous quality improvement in a manufacturing environment. * Previous work experience in an organization that supplied large OEMs. * Customer quality assurance experience. * Previous audit experience. * Experience in the automotive industry; Battery, Electronics, or Powertrain manufacturing preferred. Key Competencies: * Focuses on Quality: Drives work results with a quality focus on actions and results. * Decision Making & Analysis: Makes sound decisions based upon a mixture of data-driven analysis, expertise, experience, and judgment;