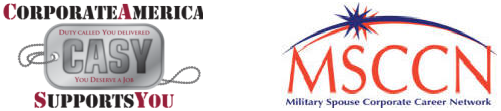
Job Information
Air Products and Chemicals, Inc. QAQC GRP Piping Inspector in KSA, United States
50014BRReq No.:50014BRJob Description and Qualifications: . POSITION SUMMARY
The QAQC Inspector – GRP / FRP is responsible to ensure that all GRP / FRP / RTR construction and commissioning activities are performed in accordance with the provisions of the Construction Quality Plan and AP Engineering Requirements.
III, NATURE AND SCOPE
Safety & Quality are very important aspect in all project phases,
Travel might require for this position both short & long business trips as needed.
IV. DIMENSIONS:
Coordinating site construction activities with Engineers / QC GRP Inspectors of EPC Sub-contractors and Client.
Working in a Mega size project
Multi- project Type: EPC Oil & Gas, Petrochemical, Infrastructure Plants
V. PRINCIPAL ACCOUNTABILITIES
An approved QAQC Inspector – GRP / FRP has the responsibility and commensurate authority to accomplish the following duties:
Reporting to the Site QAQC Department Manager
Monitoring and implementation of QMS Procedures, PQP, ITP, Method statement, Manufacturer’s Lamination Procedures & and reporting deviations from management system / contractual requirements of the projects.
Review subcontractor’s ITPs for GRP piping works
Verify qualification records of Subcontractor bonders/laminators, Supervisors and QC Inspectors if trained by the same Manufacturer that would supply GRP materials in GHE project.
Witness bonders initial pressure test.
Attend pre-construction quality meeting and Subcontractors quality meetings.
Review procedure for installation of GRP piping, lamination, and repair.
Carryout material receiving of pipes, fittings & flanges, and storage inspections of GRP lamination materials prior to application. Ensure all materials are within its validity date, dry, free of contamination and have been stored in accordance with manufacturer’s procedures and acceptance standards.
Verify pipe laying, alignment, internal cleaning as validated by survey coordinates & levels.
Verify strict implementation of environmental controls / surface preservation during lamination (i.e. use temp shelters/ sunscreen) during lamination in direct sunlight and/or windy condition to protect against contamination of in-process activities. Record dew point vs ambient temp to ensure the difference does not exceed manufacturer’s recommendation.
Perform fit-up inspections. Check lamination & fit-up crews have tolerance requirement document (i.e. maximum gap and maximum misalignment), lamination recipes, IFC drawings applicable for the type and diameter of joints they are working on.
In joint surface preparation, verify disk grit size and that surfaces have been adequately ground off
Monitor resin putty application, joint application & assembly in accordance with manufacturer’s procedure and applicable joint recipe.
Check lamination joint by dimensional and visual defects as per joint type.
Witness Barcol Hardness verification for site applied reinforcements to GRP components if / when required.
Check adhesive bonding for all joints.
Check repair of joints (if required) specific to applicable joint / resin type i.e. GRE, GRVE, GRUP etc.
Witness assembly / gasket installation and bolt-up / torque procedure by strictly following manufacturer’s tightening sequence and graduated increments with calibrated torque wrench.
Verification of cleanliness requirements for large bore internal pipe systems that are impracticable in performing water flushing prior to hydrotest.
Conduct pre-hydrotest check (line walkdown), document review & test clearance of Hydrotest Package/s approved by Engineering.
Witness pressure testing, check water quality, line water filling, venting, test manifold, pressure gauges & relief valves are calibrated. Line drained / dried after hydrotest and reinstatement.
Witness GRP Pipe Golden Joint (closure weld) in accordance with manufacturer’s procedure and project specification.
Check final survey prior to backfilling i.e. coordinates & levels.
Monitor backfilling work to ensure all materials does not contain stone that could damage GRP pipe during backfilling work.
Coordinate quality activities with subcontractors and any other individual parties who may be working on the same site.
Coordination with clients / third party, in accordance with approved ITP, for agreed witness inspections & tests.
Ensuring all equipment’s, tools and materials meet with the project quality requirements and that personnel have been adequately trained to use them safely.
Liaise with client representative concerning quality matters on site.
To be conversant with the company QHSE procedures & policies and ensure that all the people on the site observe and implement them.
Identifying near miss and nonconformities in materials, products, processes, procedures and reporting the near miss / nonconformities in the near miss / nonconformity report.
Verification of implementation of corrective & preventive actions against the nonconformities and reporting results to QA/QC Engineer and line managers, if necessary.
Notify to QA/QC Manager of any discrepancies that relate to the GRP / FRP installation if not in accordance with manufacturer’s recommendation.
Mark or remove components that are not in accordance with project standards and guidelines, provided the removal does not jeopardize piping system integrity
Reports as necessary to offer corrective actions when certain materials or fixtures do not meet project standards
Witness installation of piping accessories such as valves, fire hydrants, fire monitors, etc, conducting testing / commissioning etc.,
The candidate should be able to read P&IDs, ISO drawings.
Ensuring the preparation of final quality dossiers/test packs which should be concurrent and maintaining backups of completed quality dossiers / test packs.
Submitting weekly report and requested information/statistics QA/QC Manager.
Liaise with QAQC Manager for all aspects of quality.
This position is accountable for the following end results:
V. MINIMUM REQUIREMENTS AND QUALIFICATIONS
Degree Mechanical Engineering.
More than 15years QA/QC experience in the fiberglass industry gained from EPC projects in the capacity as Inspector or Supervisor.
Experience in shop fabrication at the FRP Manufacturing Facility is a plus (e.g. GRP vendor for GHE project)
Experience in GRP (GRE, GRVE, GRUP)
Knowledge of the ISO-9000 series International Standards
Team Player, Strong communicator written and oral
Strong and effective coordinator
Organized, disciplined, able to perform under pressure and manage multiple priorities and parallel tasks
Strong Microsoft software skills, particularly Excel
Report writing skills
Experience of working in a multicultural project team
Middle East project experience
Desirable Qualifications, Experience and Skills
Extensive experience as GRP Specialist / Consultant
Saudi Aramco CBT Passed & project Approval.
Job Title:QAQC GRP Piping InspectorEmployment Status:Fixed Term (agency) - Full Time Location:MEET-KSA-NEOM-Duba Country:Saudi ArabiaRegion:Middle East, Egypt, Turkey (MEET) Organization:Global Engrg Mfg Technology & Equipment Business Sector / Division:GEMTE MEET