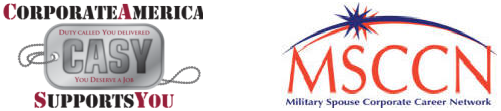
Job Information
Eaton Corporation Quality Manager in Juarez, Mexico
Eaton’s ES AMER PCS ICD division is currently seeking a Quality Manager.
What you’ll do:
This position will be located in Juarez, Mexico and is the primary lead for the functions for the site by providing quality assurance support for manufacturing, customers, suppliers and EQMS. Support programs that enhance ISO9000 preparation and readiness activities. Support the Quality Control functions and related quality assurance activities for all products manufactured by the locations. Plan and manage statistical control activities to ensure the conformance of manufactured products / equipment with customer specifications and their unique product performance requirements. Guide, direct, maintain and monitor all activities associated with the successful application of Eaton’s Quality Award process (EBE). Own and oversee and direct the activities of the test organization and collaborate with Menomonee Falls Engineering on test procedure updates and changes.
ESSENTIAL FUNCTIONS:
• Champion a culture of Safety by proactively interfacing with production, EHS, and maintenance teams to identify and appropriately mitigate hazards throughout the facility.
• Develops/improves manufacturing processes, facility enhancements, and new technologies by studying product requirements; researching, designing, modifying and testing manufacturing methods and equipment; conferring with equipment vendors.
• Advise on process capabilities and requirements for new and current products; creating training to improve the overall education of production employees.
• Develop processes and manufacturing documentation for new products. Review and update processes and manufacturing documentation of current products for improvement of process and engineering design changes to ensure ISO compliance.
• Generate and implement Engineering Change Notices, enhancing product quality and reducing product cost.
• Troubleshoot equipment, processes, and products for malfunction or problems to support daily production requirements.
• Maintains professional and technical knowledge by attending educational workshops; reviewing professional publications; participating in professional societies.
• Keeps equipment operational by coordinating maintenance and repair services; following manufacturer’s instructions and established procedures; requesting special service as needed.
• Support the Eaton Quality System. Work with Quality function to implement corrective and preventative actions.
#Li-SL4
Qualifications:
Basic Qualifications:
• Bi-Lingual (Spanish & English)
• Bachelor’s degree, preferably in Business, Manufacturing, Mechanical, or Industrial Engineering from an accredited university
• 5+ years’ experience in manufacturing methodologies
• 2+ years’ experience minimum experience in supervision
• 2+ years’ experience minimum in continuous improvement methodologies
Preferable Qualifications:
• Master’s degree in Manufacturing, Mechanical, or Industrial Engineering
• Lean Six Sigma Certification (Black Belt)
• ASQ Certified
• Knowledge of electrical power products and systems
Position Criteria:
• Process focused with continuous improvement mindset
• Ability to leverage proven tools to drive performance improvements by engaging the production work force
• Leverages data and results to develop a business case for change and drives needle moving improvements
• Demonstrated success working through others to achieve outstanding results
• Self-directed leader with a track record for driving improvements based on the needs of the business
• Business communication proficiency (written and spoken) Knowledgeable in problem solving tools such as Six Sigma, 8D, Root cause analysis, and SPC.
• Experience with ISO 9001:2000 and/or TS 16949, with knowledge of process auditing.
• Working knowledge of FMEAs, gauge R&R / MSA and control plans.
• Strong Project Management skills with the ability to prioritize
• Ability to setup and analyze multiple databases to obtain actionable information
• Excellent problem solving skills
ADDITIONAL INFORMATION:
Health and Safety Responsibilities - Employee
Know and follow the health and safety procedures and standards established for the job and for the entire facility.
Notify health and safety problems, unsafe acts detected in the area and to inform the appropriate person in charge.
Actively participate in accident, injury and illness prevention activities
Develop job safety analysis and safe work procedures.
Identify and correct hazards and unsafe conditions.
Investigate accidents, near misses or potential dangers.
We are committed to ensuring equal employment opportunities for job applicants and employees. Our recruitment processes use balanced selection criteria and avoid unlawful discrimination against applicants on the basis of their age, colour, disability, marital status, national origin, gender, gender identity, genetic information, race or racial origin, religion, sexual orientation or any other status protected or required by law.
Eaton Corporation
-
- Eaton Corporation Jobs