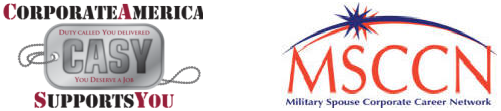
Job Information
Alamo Group Inc. Director of Manufacturing in Huntsville, Alabama
Schwarze Industries (an Alamo Group company) is currently accepting applications to fill the position of Director of Manufacturing in Huntsville, AL.
The Director of Manufacturing determines the strategic direction of the operations setting the plan for products and processes to achieve operational objectives while increasing efficiencies. The Director of Manufacturing oversees the day-to-day operations and is the champion for safety, quality, and productivity while implementing lean manufacturing principles.
The Director of Manufacturing will:
Prioritize, schedule and delegate work assignments, and directly supervise the Company’s day-to-day operations to ensure the meeting of gross profit goals. Ensure that all groups meet their performance expectations and work within their budgetary constraints.
Develop short-term and long-range strategies, plans, and budgets based on plant goals and growth objectives.
Develop, recommend, and upon approval, implement the operating budgets. Manage the budgets within the budgetary constraints. Analyze the report on variances between actual and budgeted expenditures.
Lead and mentor direct reports, building their management and decision-making skills, continuously promoting a culture that is passionate about success, and emphasizing respect, trust, and empathy in the workplace.
Drive continuous improvement initiatives focused on reducing direct labor costs using tools of lean manufacturing.
Review data and reports reflecting operating statistics. Evaluate the results of overall operations regularly and systematically and report these results to the President and senior management team.
Participate as a member of a safety leadership team to develop and maintain a comprehensive safety program that achieves 100% OSHA compliance and continuously improves the safety of the workplace.
Develop and implement procedures, policies and controls to promote efficient operations of the organization and ensure the groups follow those procedures, policies and controls.
Ensure the training of new and present employees in the processes and methods required to achieve the organization’s standards for quality, quantity, and safety, consistent with the organization’s principles.
Coordinate with the sales department to increase and/or improve gross margins through new product development, product enhancements, defining product applications, and identifying features that increase salability.
Coordinate with the Engineering department in reducing product costs through product design to improve manufacturability, reducing purchased component costs, reducing product duplication and/or combining components to increase run quantities.
Work with Department Managers and the President on capacity planning (facilities, tools and equipment, people) to meet current and future growth requirements.
Ensure compliance with all safety and work rules and regulations. Ensure the maintenance of departmental housekeeping standards.
The ideal candidate will have/be:
Knowledge and understanding of production fabrication, welding, paint, mechanical assembly, warehouse, and related processes.
Experience with developing programs to address issues involving productivity, cost improvements, and quality.
Strong leadership, organizational, and communication skills both verbally and written. Able to effectively interact at all levels of the organization.
Good team building skills; able to problem solve, persuade and motivate.
Knowledge and practical application of Lean manufacturing techniques.
Knowledge of OSHA regulations and a strong practitioner of building a safety culture.
Self-driven with strong collaborative skills.
Demonstrated ability to exhibit and model Alamo Group's Core Competencies:
Leading Change/Change Management - Balance change and continually strive to improve business performance
Leading People/Teamwork - Design and implement strategies that maximize employee's potential and foster high ethical standards
Communication - Explain, advocate and express facts and ideas in a convincing manner and negotiate with individuals and groups
Business Acumen - Understand and interprets business metrics and utilizes latest business strategies to focus on outcomes and create opportunities for success
Results Driven/Process - Make timely and effective decisions and produce results through planning and implementation of processes, systems, and programs; stressing accountability and continuous improvement
Education and Experience:
Bachelor's degree in engineering or related areas, or equivalent experience.
Minimum 7-10 years previous Manufacturing/Supervisory experience required.
Working knowledge of low volume high mix types of assembly operations
Working Conditions:
Conditions will vary between manufacturing floor and office setting.
Ability to work days, nights, overtime, and or weekends as needed.
May be required to travel at times.
Alamo Group is proud to be an Equal Employment Opportunity, Affirmative Action employer. All qualified applicants will be considered without regard to race, national origin, color, religion, age, genetics, sex, sexual orientation, gender identity or expression, disability or veteran status. We maintain a drug-free workplace and perform pre-employment substance abuse testing (where permitted by law).
Alamo Group Inc.
-
- Alamo Group Inc. Jobs