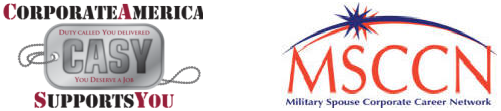
Job Information
Niagara Bottling LLC Injection Operations Manager in Diamond Bar, California
At Niagara, we’re looking for Team Members who want to be part of achieving our mission to provide our customers the highest quality most affordable bottled water.
Consider applying here, if you want to:
Work in an entrepreneurial and dynamic environment with a chance to make an impact.
Develop lasting relationships with great people.
Have the opportunity to build a satisfying career.
We offer competitive compensation and benefits packages for our Team Members.
Injection Operations Manager
The Injection Operations Manager is responsible for defining and executing the injection strategy in order to improve overall injection molding operational effectiveness, which includes Safety, Quality, and Performance. This role will be involved in the development of operational excellence and best practices, preventive and predictive maintenance programs, troubleshooting guides, inventory control best practices and overall optimization of injection molding operations.
This role will be working with all phases of Injection Operations (Production, Quality, Tech. Engineering, Materials Engineering, Asset Management, SRM, Training, etc.) in order to execute the injection operations strategy.
Essential Functions
Provide functional and technical leadership on projects across all aspects of injection molding principles (Materials, Processing, Equipment) in order to achieve operational excellence in Injection Molding at Niagara.
Be the Injection expert, gaining a full understanding of all components of each operation, in detail, including but not limited to preform injection systems, closure injection systems and supporting auxiliary systems.
Mentor plant injection molding leaders, Maintenance Managers, Quality Managers and SMTs and Injection Managers in partnership with the Plant Directors on optimal injection practices.
Develop effective and efficient working relationships with both internal teams and external partners.
Provide continuous support to all plants for systemic injection molding issues across Niagara.
Collaborate with vendors, corporate project managers and operations to develop injection molding best practices.
Work with appropriate cross functional teams to identify and implement process improvements to improve injection molding OEE, Quality, Availability, and Safety.
Identify cost savings opportunities and develop business plans to realize the savings.
Work closely with the facilities to implement injection strategies and best practices.
Identify safety opportunities and communicate to the appropriate stakeholders for resolution.
Support the plants in maintaining world class safety, quality, line performance and cost metrics in the injection molding operations.
Analyze operational and quality data to look at trends and proactively find/solve problems and make recommendations for improved operations.
Facilitate and support Industry 4.0, condition-based maintenance and other innovative operational and maintenance-based programs.
Optimize service and costs in injection manufacturing.
Set team and individual goals for injection plant operations.
Support and optimize regularly scheduled audits of each operation to assess effectiveness and efficiency and work with the teams to improve deficient areas.
Identify new technology to further improve the overall injection molding capabilities.
Travel 75% of the time
Please note this job description is not designed to contain a comprehensive list of activities, duties or responsibilities that are required of the employee for this job. Duties, responsibilities and activities may change at any time with or without prior notice.
Competencies
Ability to negotiate, collaborate and influence
Ability to analyze data and find/mitigate risk
Results driven and ability to communicate
Experience in developing high speed injection molding processes with HDPE and PET materials
Experience in injection mold design including hot runner systems
Ability to use technical problem solving techniques to quickly troubleshoot and solve injection molding process issues
Ability to identify weak spots in a process to improve efficiency
Great planning and project management skills
Ability to work in a fast-paced environment
Travel 75% of the time
Qualifications
Minimum Qualifications:
6 Years - Experience in Field or similar manufacturing environment
6 Years - Experience in Position
6 Years - Experience managing people/projects
*experience may include a combination of work experience and education
Preferred Qualifications:
10+ Years - Experience in Field or similar manufacturing environment
10+ Years - Experience working in Position
10+ Years - Experience managing people/projects
*experience may include a combination of work experience and education
Education
Preferred:
Bachelor's Degree.
Typical Compensation Range
Pay Rate Type: Salary
$103,207.00 - $144,490.00 / Yearly
Bonus Target: 10% Annual
Benefits
https://careers.niagarawater.com/us/en/benefits
Any employment agency, person or entity that submits a résumé into this career site or to a hiring manager does so with the understanding that the applicant's résumé will become the property of Niagara Bottling, LLC. Niagara Bottling, LLC will have the right to hire that applicant at its discretion without any fee owed to the submitting employment agency, person or entity.
Employment agencies that have fee agreements with Niagara Bottling, LLC and have been engaged on a search shall submit résumé to the designated Niagara Bottling, LLC recruiter or, upon authorization, submit résumé into this career site to be eligible for placement fees.
Niagara Bottling, LLC has been family owned and operated since 1963. Niagara is a leading bottled water manufacturer in the U.S., supplying major retailers across the nation. With incredible growth over the past several years, the career possibilities at Niagara are endless!
Niagara’s culture is fast-paced, innovative and intensely collaborative. Our Team Members are passionate, driven and always find a way to get the job done. We work hard and play hard while staying true to our family atmosphere.
From competitive benefits and retirement options to educational reimbursements, ongoing training courses and exciting career advancement opportunities, at Niagara we truly take care of our Team Members.
We hope that you consider joining our Niagara family!
Niagara Bottling LLC is an Equal Opportunity Employer that does not discriminate on the basis of race, color, religion, sex, age, sexual orientation, gender identity and/or expression, national origin, veteran status or disability in relation to our recruiting, hiring, and promoting practices.