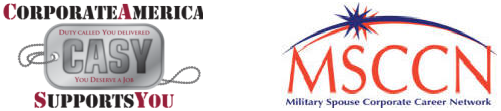
Job Information
Construction Specialties, Inc. Master Scheduler in Denton, Texas
Master Scheduler - ( 230009F )
Description
CONSTRUCTION SPECIALTIES, INC.
Founded in 1948, Construction Specialties (CS) is a specialty building products manufacturer. CS provides solutions to building challenges that architects, designers, building owners, facility managers, and contractors face every day. Since inventing the first extruded louver, CS has become a global leader in all our product categories. Our products are a part of some of the most iconic buildings around the world–from the world’s tallest tower, Burj Khalifa in Dubai, to the Oculus at the World Trade Center Transit Hub in Manhattan. If you want to work in an inspiring atmosphere and collaborate with customers and colleagues to solve challenges, we're the right place for you. CS: People. Buildings. Better.
Equal opportunity is not only the law but is the basis of how we ensure that our workplace fosters an environment of fairness, equality, and respect. It is the policy of Construction Specialties to provide equal employment opportunity (EEO) to all persons regardless of age, color, national origin, citizenship status, physical or mental disability, race, religion, creed, gender, sex, sexual orientation, gender identity and/or expression, genetic information, marital status, status with regard to public assistance, veteran status, or any other characteristic protected by applicable federal, state or local law. In addition, Construction Specialties will provide reasonable accommodations for qualified individuals with disabilities unless the accommodation would impose an undue hardship on our operations.
SCOPE OF POSITION :
The Master Scheduler plans, establishes, and oversees production schedules to meet customer demands. Develops master production schedules in accordance with sales forecast, plant and employee capacity, and new business opportunities. Has responsibility to decide operation plan for made-to-stock or made-to-order.
ESSENTIAL DUTIES AND RESPONSIBILITIES :
To perform this job successfully, an individual must be able to perform each essential duty satisfactorily. The requirements listed below are representative of the knowledge, skill, and/or ability required. Reasonable accommodations may be made to enable individuals with disabilities to perform the essential functions, including but not necessarily limited to the following:
Responsible for the development, maintenance, and communication of the Master Production Schedule (MPS)
Responsible for product lead times, on time delivery, and production schedule maintenance
Reviews material and capacity changes required to meet lead-time changes to the schedule as requested by sales or production. Makes recommendations for earliest achievable dates to maximize machine and work center usage
Manages top-level capacity reviews with support of production leadership
Manages master distribution schedule for assigned facilities
Supervisors and monitors completion of and adherence to the work orders and schedules to ensure internal and external customer orders are satisfied. Adequately communicates schedule shortfalls to the appropriate people.
Regularly updates information and performs date maintenance in the ERP system to provide accurate and timely availability of information.
Recommends and selects alternative schedules to address medium and long-range capacity constraints or material availability issues in a manner that minimizes disruptions, schedule changes, and maintains production up time.
Contributes to Sales, Inventory, and Operations Planning (SIOP). Leads additional planning meetings with stakeholder group.
Develop and present schedule metrics for varying levels of leadership. Support operational and financial metrics
Manage schedule risk analysis and conduct critical path analysis
Develop and support strategic scheduling activities to achieve enterprise program goals
Ensures conformance to all aspects of the ISO 14001 standard, CTPAT, and Construction Specialties’ Environmental Management System (EMS), including its environmental policy while performing job functions that may have a significant impact on the environment.
Performs related work as apparent or assigned by supervisor/manager
Qualifications
KNOWLEDGE/ SKILLS/ EXPERIENCE/ EDUCATION : (Minimum Education and/or Experience required)
Bachelor's or Graduate's Degree in business, computer science, engineering
5 years or more production planning experience with thorough knowledge of manufacturing, purchasing, materials, and production processes. Additional experience instead of a degree will be considered.
Operations experience in scheduling CNC machine tools, welding, and fabrication processes
APICS certification (CPIM or CSCP) preferred or strong familiarity with APICS terminology and working procedures is necessary.
Must have experience implementing and running an MRP/ERP system.
Should have experience with VPL, IMS, and or WMS systems
Excellent organizational skills that reflect the ability to perform and prioritize multiple tasks seamlessly with excellent attention to detail.
Ability to work effectively both independently and in a team environment.
Demonstrate the ability to extract data from databases and spreadsheets and perform accurate statistical analysis and summary reports.
Proficient in Microsoft Office applications.
Experience in coordinating and organizing complex activities involving several different people, groups, and organizations
COMPETENCIES :
People Leadership Skills
Safety
Organization and efficiency
Communication Skills
SUPERVISORY RESPONSIBILITIES :
- None
Primary Location : US-TX-Denton
: Supply Chain
Travel : No
Employee Type: : Full-Time Regular
Req ID: 230009F
Construction Specialties, Inc.
-
- Construction Specialties, Inc. Jobs