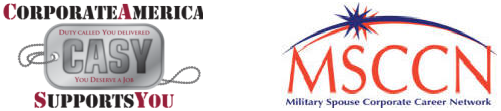
Job Information
ArdaghGroup Lean CI Supervisor - 1052362501-4633 in Chicago, Illinois
This job was posted by https://illinoisjoblink.illinois.gov : For more information, please see: https://illinoisjoblink.illinois.gov/jobs/11847463 Primary Purpose:
To drive creation and execution of plant continuous improvement initiatives, delivering short and long-term improvement results for all business objectives, including safety, quality, and productivity. Success is measured by the leader\'s ability to develop a continuous improvement culture by actively educating and engaging teams to achieve tangible results utilizing structured Lean and Six Sigma tools within the DMAIC method. The position champions the use of continuous improvement and problem-solving tools to meet financial goals. This person is the mentor and change agent for developing a continuous and quality improvement culture across all plant levels and all departments.
Responsibilities & Duties:
- Train, coach, support, and lead all levels of the plant in the
effective implementation and use of Lean and Six Sigma continuous
improvement tools and methods which include:
- Plant Performance Workshops
- Kaizen\'s, Workshops, Classroom Training
- Certifications
- Continuous Improvement Steering Committees, and Teams
- Audits, and facilitation of audit gap closing plan
- Scorecards: Development, maintenance, reporting, improvement
- Creation and improvements to Standard Work, SOP\'s, Training materials, etc.
- Project Administration: hopper, selection, mentoring, tracking, reporting, ptracker
- Engaging Team Members and process owners as the primary input source for all plant continuous improvement activities
- Create and maintain continuous improvement culture by developing, implementing, and supporting daily CI methods within all levels and all departments of the plant
- Facilitate the 8D problem solving process on all plant accidents, and safety continuous improvement efforts
- Along with the Plant Manager, responsible for driving and facilitating plant Lean Six Sigma deployment progress and continuous improvement through the plant LSS Tool Champions (5S, TPM, SMED, Six Sigma, Culture) as measured by the LSS Audit.
- Along with LSS Champion and Plant Manager, create an annual, and 3-5 year Plant Continuous Improvement Strategic Plan consistent with the LSS Audit (5S, TPM, SMED, Six Sigma, and Culture). Execute the Continuous Improvement Strategic Plan
- Ensure all projects align with business objectives, and KPI\'s
- Support and mentor project team leaders and their project teams
- Successfully deliver 2 assigned plant improvement projects per year
- Monthly monitoring, tracking, and reporting progress on all Lean initiatives, and Six Sigma projects
- Closing the trained vs. certified gap for plant Lean and Six Sigma trainees
- Facilitate customer complaint reduction and elimination through 8D and Continuous Improvement meetings with Team Members, Plant Manager, Quality Manager, Production Manager, and Team Leads.
- Facilitate and help lead the Plant Performance Workshops, which supports the plant\'s business objectives through CI project identification and deployment process
- Mentor plant leadership teams in implementing a focused CI culture that drives waste elimination and a relentless focus on customer needs.
- Challenge the status quo and be a change agent for the business.
- Mentor Plant leadership team members to ensure they possess the skills and capabilities to drive for results, and to ensure that CI / Lean thinking and customer focus is applied to all business decisions
- Ensure Plant has current and future state Value Stream Maps to drive transformation and an enterprise view of waste elimination. Create an annual VSM review.
- Train all levels of leadership teams on CI / Lean tools, processes, systems, and culture.
- Champion productivity efforts and initiatives to achieve budget and targets
- Ensure that standard operating procedures exist to meet both the short term and long-term needs of the business
- Drive, monitor, and support best practice utilization by ensuring department managers and their departments are in alignment with OSG best practices
- Champion best practice / kaizen utilization to assist in meeting Plant and business unit objectives if no OSG best practices exist
- Support and help lead plant production schedule and supply chain optimization, through the elimination of waste, unevenness, and overburden
- Assist with specific and focused projects in the plant/region/business unit where required.
- Utilize the DMAIC to drive manufacturing excellence and continuous improvement in all key processes
- Teach Plant leadership team members how to incorporate CI / Lean tools, processes and systems into their areas of responsibility through coordination of six
- Effectively invest time to coach the organization, direct reports, peers, and plant leadership to have the capability to drive improved employee engagement
- Fully support and assist LSS Champion and LSS TPM Champion in all continuous improvement efforts (Training, Kaizen\'s, Workshops, Follow-ups, etc.) as requested and required
Direct Reports: None.
\<