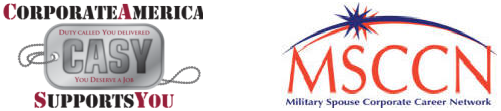
Job Information
The Dannon Company Quality Systems Specialist in Chatsworth, New Jersey
At Danone, Manufacturing the best products and supplying them to meet demand is a key driver for our plant teams. We are currently looking to hire a Quality Systems Specialist based in our Chatsworth, California manufacturing plant! In this role, you will support the implementation of the Danone North America Quality Assurance standards through technical guidance, analysis, and leadership to continuously improve quality performance. The Quality Systems specials supports in assessments and improvements in the areas of food safety systems, Quality procedures and documentation.
Danone North America additionally offers a strong benefits package including Medical, Dental, Vision, Prescription Drug Coverage, Wellness Program, Life Insurance, Tuition Reimbursement, Paid Time Off, and Paid Parental Bonding Leave, among other benefit plan options.
In this role, you will be responsible for the following:
- Provide Quality and Food Safety technical guidance, analysis, and leadership driving improvements in sanitation processes/systems, quality and food safety systems.
- Compile and analyze KPIs indicative of production line health (quality performance, microbiological quality, preventive maintenance, sanitation effectiveness, etc.) and create reports of trends for improvement as needed.
- Support the analysis of customer and consumer feedback to identify improvement opportunities.
- Provide training and mentoring to operations teams on food safety and quality related topics to develop a strong quality culture.
- Support the validation of cleaning effectiveness via the sanitation ("Neptune") program.
- Support the development of quality, food safety and sanitation SOPs.
- Manage and troubleshoot non-conformances (raw materials, packaging, product, environmental monitoring, etc.) and drive root cause analysis. Assign corrective action, collaborate with supply-quality and other functions, and follow-up on completion.
- Support plant GFSI and FSMA initiatives and participate as support during audits.
- Support change management processes related to new products, packaging, equipment, and processes.
Disclaimer
The above information on this description has been designed to indicate the general nature and level of work performed by employees within this classification. It is not designed to contain or be interpreted as a comprehensive inventory of all duties, responsibilities and qualifications required of employees assigned to this job.
Nothing in this job description restricts Danone North America's rights to assign or reassign duties and responsibility to this job at any time.
Danone North America provides equal employment opportunities to all employees and applicants for employment without regard to sex, race, color, religion, marital status, national origin, age, sexual orientation, disability, veteran status, p regnancy, or any other factor that may be protected by law. This policy extends to all employees and includes all aspects of the employment relationship. Danone North America is an Affirmative Action/Equal Opportunity Employer.
Education and Experience (Requirements):
- Bachelor's Degree in a science related field (Microbiology, Food Safety, or similar) or other technical discipline.
- 0-3 years of experience in the dairy/food/beverage manufacturing industry, including supervisory experience.
Knowledge, Skills and Abilities:
- Preferred experience using structured and data driven problem-solving techniques (RCPS, DMAIC, Six-sigma, LEAN, etc.).
- Excellent communication, leadership and interpersonal skills.
- The ability to influence others and be a team player.
- The ability to develop/implement core work practices and standards that ensure excellence in quality.
- The ability to rapidly assess, analyze, and quickly resolve complicated quality problems with little initial information or direction and with varying degrees of ambiguity.
- The ability to multitask and manage priorities while allocating time to long-term, quality continuous improvement projects.
- Strong "self-management" skills and be comfortable working with minimal supervision.
- Established project management skills. Must bring leadership, interpersonal and communication skills required to interact with various levels of plant and corporate personnel and influence others.
- Willingness to work flexible schedules as needed to support 6-day per week, 24-hour per day production facilities. Work schedules could include occasional off-shift or weekend work.
At Danone North America, you'll work with some of the best-known food and beverage brands in the world like Activia, Silk, Two Good, Oikos, evian, and Happy Family. You'll be part of one of the largest Certified B Corps in the world, working together to make sure our brands create real benefits for people, communities, and the planet. We have 6,000+ employees across the U.S. and Canada. Come join our movement for a healthier world: One Planet. One Health BY YOU.
Danone North America doesn't just welcome what makes you unique, we value it. We're proud to be an equal opportunity and affirmative action employer. All hires to our team are based on qualifications, merit and business needs. We recruit, employ, train and promote regardless of race, color, religion, disability, sex, sexual orientation, gender identity, national origin, age, veteran status, genetic characteristic or any other protected status. Faithful to our values of openness and humanism, all of our employees share in the commitment to engage one another with dignity and respect. http://www.dol.gov/ofccp/regs/compliance/posters/pdf/eeopost.pdf
Dannon is an equal employment and affirmative action employer. All qualified applicants will receive consideration without regard to race, color, religion, disability, sex, sexual orientation, gender identity, national origin, age, veteran status, genetic characteristic or any other unlawful criterion.