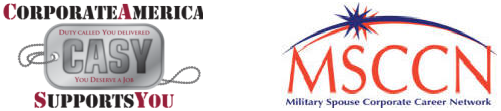
Job Information
Berry Global Scheduler in BLOOMINGTON, Indiana
Overview
About Berry
At Berry Global Group, Inc. (NYSE: BERY), we create innovative packaging and engineered products that we believe make life better for people and the planet. We do this every day by leveraging our unmatched global capabilities, sustainability leadership, and deep innovation expertise to serve customers of all sizes around the world. Harnessing the strength in our diversity and industry-leading talent of over 40,000 global employees across more than 250 locations, we partner with customers to develop, design, and manufacture innovative products with an eye toward the circular economy. The challenges we solve and the innovations we pioneer benefit our customers at every stage of their journey. For more information, visit our website , or connect with us on LinkedIn or Twitter.
Responsibilities
Major Responsibilities
Create and maintain production schedules in order to ensure that all Company goals are achieved and deadlines are met.
Es sential Duties and Responsibilities include the following. Other duties may be assigned.
Safety Management
Perform duties in a safe manner; Acts as a role model for Safety. Participates in and/or leads teams focused on safety issues.
Participations and promotes the Safety Behavior Program with all production employees; reviews issues with the EHS Manager and Production Management team to ensure that all issues brought up by employed are addressed in a timely ma nner.
Planning and Scheduling Management
Schedule the production process and production departments by material, employee and equipment availability to minimize company costs.
Monitor workflow and schedules to ensure on-time delivery.
Developed effective scheduling process and implement process improvements.
Review production specifications in order to identify and report plant capacity constraints.
Analyze and address production issues in a timely manner including manpower and material shortages and work with relevant departments to resolve.
Manages the on hand packaging, film inventory and resin on a regular basis. Follows up on inventory discrepancies and works with Production on corrective measures.
Provide daily production status updates for Production Team.
Issue priority list to guide the production floor.
Alert Customer Service of any delays in meeting the current demands.
Coordinate with Production Team to develop and execute production plan.
Work with Managers to develop potential solutions to improve production performance.
Coordinate with Production, Purchasing and Finance teams to develop and maintain scheduling parameters.
Work with Maintenance Department to coordinate preventive maintenance, emergency maintenance and capital projects.
Generate various inventory related reports to Managers for critical decision-making purposes (i.e. inventory projections, tableau, DOH).
Oversees shared resin and material supply between Bloomington and Odon plants and enters inter-company transfers as needed.
Review various reports daily adding or modifying work orders as needed.
Provide capacity updates for new business and increased sales.
Participate in regular phone and web based conferences.
Use software to generate reports and manage schedules.
Work with Corporate Purchasing to coordinate materials purchases and delivery.
Participates in and leads employee driven teams to address scrap, quality, safety, or other production related issues; actively participates in cost savings activities
Production and Materials Management
Coordinates with Technical Manager, PDMs, and Process Team on new product trials and the introduction of new materials.
Initiates resin substitutions based on resin availability and qualification.
Monitors resin inventories; forecasts resin consumption.
Communicates resin purchase needs to corporate resin buyer.
Works with Lead Resin Handler to manage Materials flow between the Warehouse and Plant.
Qualifications
To perform this job successfully, and individual must be able to perform each essential duty satisfactorily. The requirements listed below are representative of knowledge, skill, and/or ability required. Reasonable accommodations may be made to enable individuals with disabilities to perform the essential functions.
Education and/or Experience
High School education required. Associates degree or equivalent work experience preferred. Experience in a manufacturing setting, preferably manufacturing scheduling experience. 3-5 years blown film extrusion/conversion experience and ISO 9000 experience preferred.
Competencies
To perform the job successfully, an individual should demonstrate the following competencies:
Safety and Security – Embodies plant wide commitment for a safe workplace; acts as a role model on safety matters.
Quality Focus - Is dedicated to providing the highest quality products and services which meet the needs and requirements of internal and external customers; is willing to re-engineer processes from scratch; creates a learning environment leading to the most efficient and effective work processes; looks for ways to improve and promote quality; demonstrates accuracy and thoroughness; monitors own work to ensure quality.
Visionary Leadership – Inspires respect and trust; mobilizes others to fulfill the vision; provides vision and inspiration to peers and subordinates.
Change Management – Communicates changes effectively; builds commitment and overcomes resistance; prepares and supports those affected by change.
Business Acumen - Understands business implications of decisions; Demonstrates knowledge of company financial measures; Aligns work with strategic goals.
Organizational Support – Supports organization’s goals and values; Supports affirmative action and respects diversity, promotes quality and safe work habits.
Directing Others – Good at establishing clear directions; sets stretching objectives; distributes the workload appropriately; lays out work in a well-planned and organized manner; maintains two-way dialogue with others on work and results; brings out the best in people; is a clear communicator.
Other Skills and Abilities
Ability to organize and prioritize work activities and to handle multiple projects simultaneously
Ability to make practical decisions without appreciable direction or advance preparation
Computer literate with a working knowledge of Microsoft Office desktop applications and the ability to learn and operate JDE.
Ability to participate in multiple Plant Teams such as Continues Improvement and ISO Auditor.
Physical Demands
The physical demands described here are representative of those that must be met by an employee to successfully perform the essential functions of this job. Reasonable accommodations may be made to enable individuals with disabilities to perform the essential functions.
While performing the duties of this job, the employee is regularly to talk, hear, sit, walk, stand, and use hands and fingers. The employee must occasionally lift and/or move up to 10 pounds.
We are an Equal Opportunity Employer and do not discriminate against any employee or applicant for employment because of race, color, sex, age, national origin, religion, sexual orientation, gender identity, status as a veteran, and basis of disability or any other federal, state or local protected class. (https://careers-berryglobal.icims.com/jobs/23891/scheduler/job?mode=apply&apply=yes&in_iframe=1&hashed=-1834445335)
Location US-IN-BLOOMINGTON | US-IN-ODON
Job ID 2024-23891
Position Type Regular Full-Time
Category Supply Chain
Location : Address 4100 PROFILE PKWY
Additional Locations US-IN-ODON
Berry Global
-
- Berry Global Jobs